Until recently, augmented reality hasn’t quite lived up to its hype. Since 2010, augmented reality and its immersive cousin, virtual reality, have attracted billions in investments from venture capitalists, as well as plenty of headlines. The latter often focused on entertainment, but for businesses, the real draw of AR lay in its ability to radically improve manufacturing, including employee training and productivity. Yet, for years, many enterprises were slow to adopt the technology because of seemingly insurmountable hurdles related to system integration, hardware and software.
That’s finally changing. Much-publicized advancements in hardware (think smart glasses and headsets) helped bring AR to the top of its game, but we’re focusing on another key part of the AR puzzle: easily deployable and scalable software solutions for large enterprises, often courtesy of promising startups. We’re especially excited about what AR can do for commercial aviation. But first, some background…
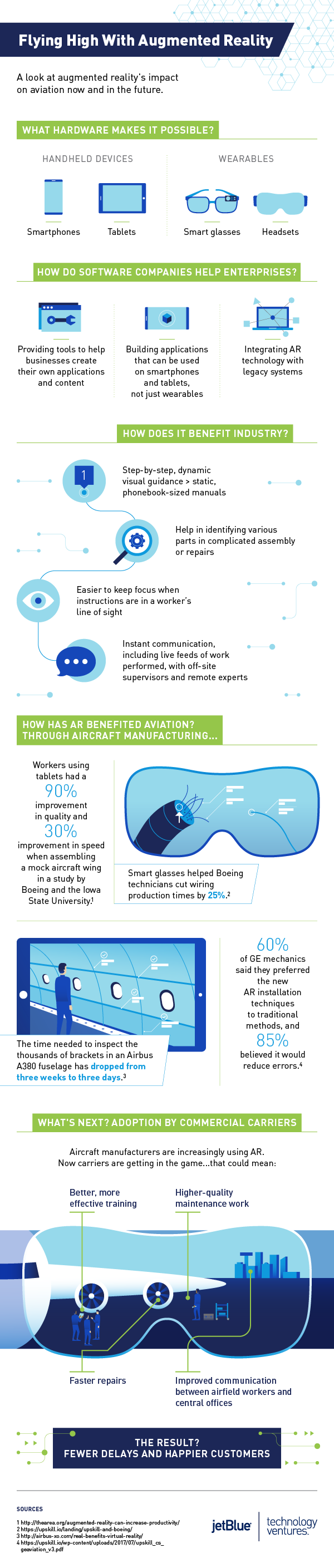
Understanding AR
AR is often mentioned in the same breath in virtual reality, but it’s important to understand the difference between the two. In augmented reality, users see digital data overlaid on the real world. In virtual reality, the world experienced by users is entirely synthetic. Both technologies fall within the broader category of mixed reality, according to Alexandre Godin, who coordinates mixed reality applications at Airbus. “Mixed reality is a continuum of technology, and on one side you have augmented reality, which is grounded in the physical world, and on the other side, you have virtual reality, which is fully synthetic. Both are very complementary and address different business needs,” Godin says.
As investors, our interests lie mainly in augmented reality. Why? Because of its ability to augment workflows to increase human productivity and improve a company’s bottom line. Combining AR with technologies like artificial intelligence will be even more transformative and empowering to the industrial workforce.
To understand the power of AR, it’s important to take stock of where we are without it.
In traditional manufacturing settings, workers must constantly shift focus between their work and written instructions. They may spend far too long flipping through phone-book-size manuals or scrolling down screens to find relevant information. They may make mistakes if they read something incorrectly or have trouble understanding a two-dimensional drawing.
AR can bridge the gap between the data once confined to paper and the physical world before us. “In true augmented reality, there is a spatial understanding and recognition of the scene, so to speak. As you move around, the CAD drawings that are overlaid move with the part, so it feels seamless,” explains Scott Terry, an industrial engineer at Boeing. Terry and his Boeing colleague, design and analysis engineer Paul Davies, worked on a study with Iowa State University that contrasted AR-guided assembly with traditional assembly, and the results were dramatic.
As part of the study, workers were selected and separated into three groups, and asked to assemble parts of a wing structure that was unfamiliar to them. The process took 50 steps for nearly 30 different parts. One group followed instructions from a PDF file provided on a desktop computer screen. A second group used a PDF file displayed on a tablet that they could carry along with them. A third group used tablets displaying AR software featuring guided steps with graphical overlays. Researchers found that the AR group made significantly fewer errors in assembly than the non-AR groups — the quality of the assembly was 90 percent better for the AR group than the desktop group, in particular. The AR group also showed a reduction in assembly time over the desktop and built the wing much faster — about 30 percent faster than the desktop group.
The study also illustrated how AR can improve training. The workers in the study had never assembled that particular wing structure before. Researchers found that presenting instructions with the help of augmented reality helped study participants gain a faster understanding of the work at hand. Outside of academic studies, some companies are already using AR to improve training. Agco, an agricultural equipment manufacturer, found that taking advantage of AR tools cut training times in half, according to the Society for Human Resource Management.
AR technology can also help industries more efficiently verify the completion of important tasks and improve communication. Cameras and other features of AR hardware can take snapshots and record the work being performed and also stream live feeds to off-site supervisors and experts. It’s a feature offered by startups like Optech4D and ScopeAR. In one use case for the latter, a large industrial supplier used ScopeAR’s technology to help customers avoid their regular visits to a service center for equipment inspections. Instead, the customers contacted the supplier’s service center through ScopeAR tools to perform inspections remotely, saving time and money.
What’s Happening Now
Fortune 500 firms have taken notice of the power of AR, with everyone from General Motors to DHL using the technology to improve workforce efficiency and productivity. Of particular interest to us has been AR’s steady ascendance among aircraft manufacturers. Multiple pilot programs by major OEMs have yielded impressive results. Since 2011, Airbus has used AR applications on tablets to help technicians charged with inspecting brackets on the Airbus A380 aircraft. The time needed to inspect the thousands of brackets in an Airbus A380 fuselage dropped from three weeks to three days.
GE combined three technologies — smart glasses, Skylight software from the startup Upskill and a Wi-Fi-enabled torque wrench — to aid in the installation of B-nuts that connect aircraft engine fluid lines and hoses. Correct installation of B-nuts is critical to avoiding mechanical problems on planes. Instructions for installation were provided on the glasses, but the connectivity with the wrench added another dimension: The torque that mechanics applied was measured in real time, and the mechanics were notified on their glasses when the torque was in the correct range. Sixty percent of GE mechanics said they preferred the new installation technique to traditional methods, and 85 percent believed it would reduce errors.
While Airbus has developed its own AR production studio internally to drive its strategy and develop applications, much of the AR software in use today has been developed by independent software companies. Startups in the space, in particular, aren’t just creating custom content for manufacturers; they’re also developing tools that allow manufacturers to produce content of their own. Upskill has developed a “drag-and-drop interface” that empowers nontechnical personnel to build the applications they need, making it easier and less expensive to pilot new AR use cases within a business. ScopeAR also targets users without coding skills, allowing them to not only create content but also to share it with colleagues, who can provide feedback through in-app annotation tools. In addition, startups are providing services to integrate legacy systems with AR technologies and deploy AR solutions to employees (and their devices) around the world.
To be sure, AR technology is far from perfect. AR solutions are, at least for now, cost-prohibitive to some companies and require immense connectivity and bandwidth. Battery-life limitations and concerns about the comfort of wearables are also discouraging to some would-be users. Such challenges notwithstanding, however, the list of enterprises employing AR is growing longer every day.
The Potential for Commercial Aviation
As aircraft OEMs continue to incorporate AR, customers like commercial airlines will benefit. Airlines can expect aircraft and parts that are built faster and better. Manufacturers’ maintenance services will also improve, which may reduce the amount of time an aircraft part is out of service, meaning airlines may need fewer spare parts in general. “It can take several months to overhaul an engine,” explains Ted Robertson, engineering manager at GE Aviation. “Time is money. If I can overhaul an engine 10 percent faster, that’s 10 percent fewer spare engines [that an airline] has to rotate among the fleet.”
Airlines also stand to benefit more directly from AR. We are on the cusp of airlines adopting AR into their own operations — adoptions that will be made smoother with the help of enterprise software providers. We’re confident that in the near future, airline trainees and mechanics, much like OEM technicians today, will be able to view digital data and schematics overlaid on real-life aircraft equipment, guiding them through faster, more accurate repairs and maintenance. If they need additional assistance, they will call remote experts and share live feeds through the devices. And the devices’ recording capabilities and connectivity mean that the completion of repairs and other tasks can be swiftly verified by off-site supervisors. Ultimately, the resulting improvements in efficiency and accuracy could mean fewer equipment breakdowns, quicker repairs and fewer flight delays.
Both in aviation and beyond, the benefits of augmented reality have proven to be game-changing and new tools offered by AR startups are making it easier than ever for businesses to adopt the technology. Meanwhile, investors like us can be certain of one particular reality: When it comes to AR, it’s time to believe the hype.